Die Casting Defects: Understanding and Addressing Common Issues
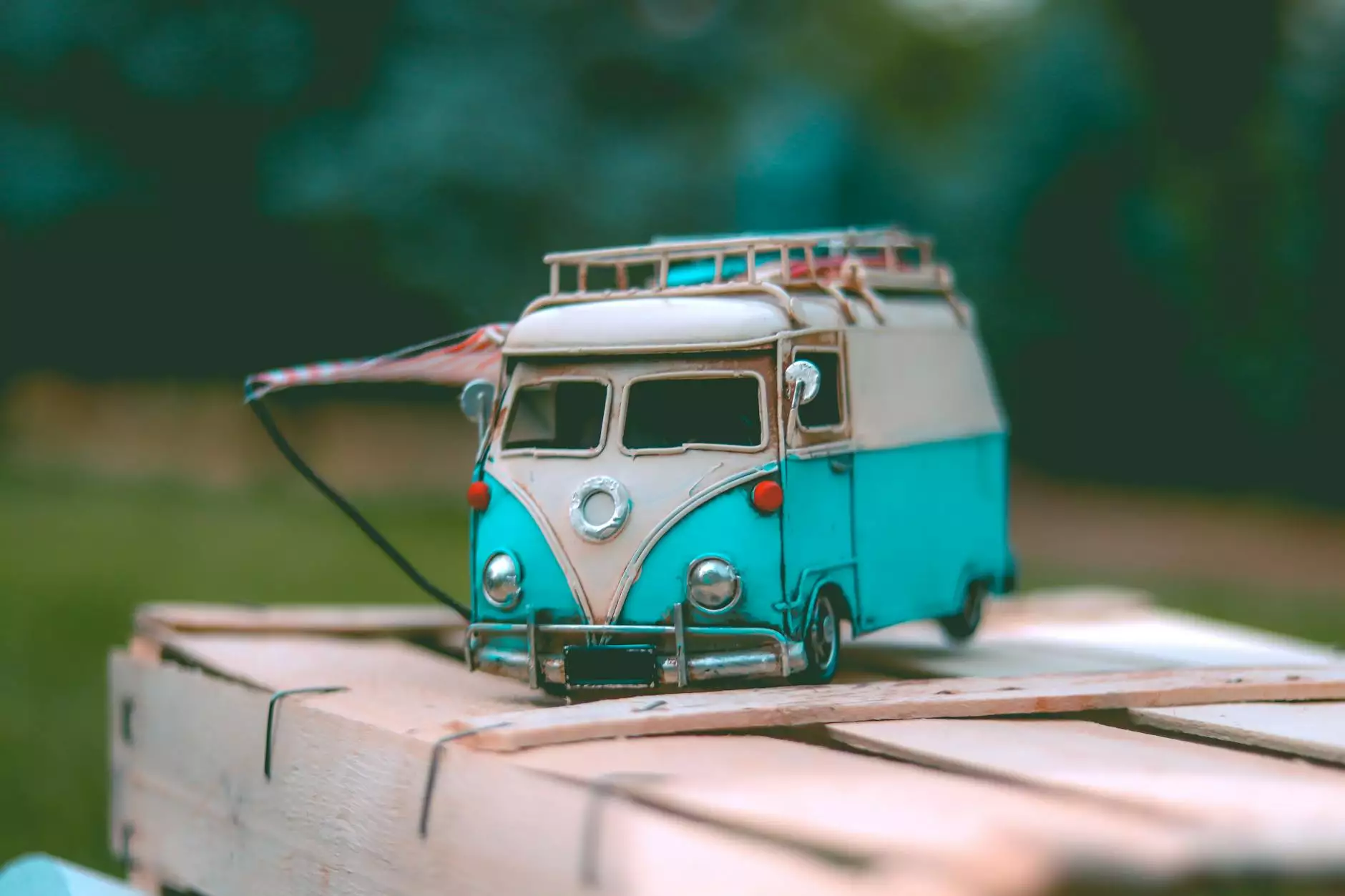
Introduction
In the fast-paced world of the Home & Garden and Appliances industry, die casting is a popular manufacturing process used to create high-quality, durable products. However, even with advancements in technology and production techniques, die casting defects can still occur and affect the overall product quality. In this article, we will explore the different types of die casting defects, their causes, and how to effectively address them.
1. Surface Defects
Surface defects are commonly encountered in die casting and can have a negative impact on both aesthetics and functionality. The most common surface defects include:
- Porosity
- Flaws and cracks
- Blistering and bubbling
- Flash
- Wrinkling
- Staining and discoloration
These defects may be caused by factors such as inadequate venting, improper die design, or suboptimal operating conditions. To prevent and address surface defects, manufacturers need to prioritize quality control measures, optimize tooling designs, ensure proper injection parameters, and regularly inspect the die casting process.
2. Dimensional Defects
Dimensional defects refer to variations in the size and shape of die cast products. These defects can lead to improper fitment, assembly difficulties, or compromised functionality. Common dimensional defects include:
- Warpage and distortion
- Underfill and shrinkage
- Short shots and undercuts
- Gating and venting-related issues
To minimize dimensional defects, manufacturers should carefully analyze and optimize die designs, conduct thorough simulations, and fine-tune process parameters. Additionally, regular maintenance and calibration of equipment are crucial for ensuring consistent castings.
3. Mechanical Defects
Mechanical defects affect the mechanical properties and structural integrity of die cast products. These defects can compromise the product's strength, durability, or functionality. Common mechanical defects include:
- Cracks and fractures
- Brittleness and weakness
- Deformation
- Incomplete filling
- Cold shuts and cold flow
To address mechanical defects, careful material selection, precise control of process parameters, and regular quality testing are essential. Advanced technologies like computer-aided engineering (CAE) and finite element analysis (FEA) can be employed to simulate and optimize the mechanical behavior of die cast products.
4. Casting Integrity Defects
Casting integrity defects refer to issues that compromise the overall integrity of die cast products. These defects can result in leakage, reduced performance, or complete failure of the product. Common casting integrity defects include:
- Porosity and gas entrapment
- Inclusions and foreign objects
- Delamination and layer separation
- Metallic contamination
- Corrosion and oxidation
Thorough inspection and testing throughout the die casting process, including material analysis, proper melt treatment, and adequate mold maintenance, are crucial for preventing and addressing casting integrity defects. Implementation of quality assurance systems and strict adherence to industry standards can significantly improve overall casting quality.
Conclusion
Die casting defects can have a significant impact on the overall quality and performance of products in the Home & Garden and Appliances industry. By understanding the different types of defects, their causes, and implementing appropriate preventive measures, manufacturers can greatly enhance product reliability and customer satisfaction. It is important to prioritize continuous improvement, invest in advanced technologies, and engage in regular training to stay at the forefront of die casting processes. By doing so, businesses can ensure their products surpass customer expectations, gain a competitive edge, and sustain long-term success.