Understanding the Significance of Silicone Injection Machines in Modern Manufacturing
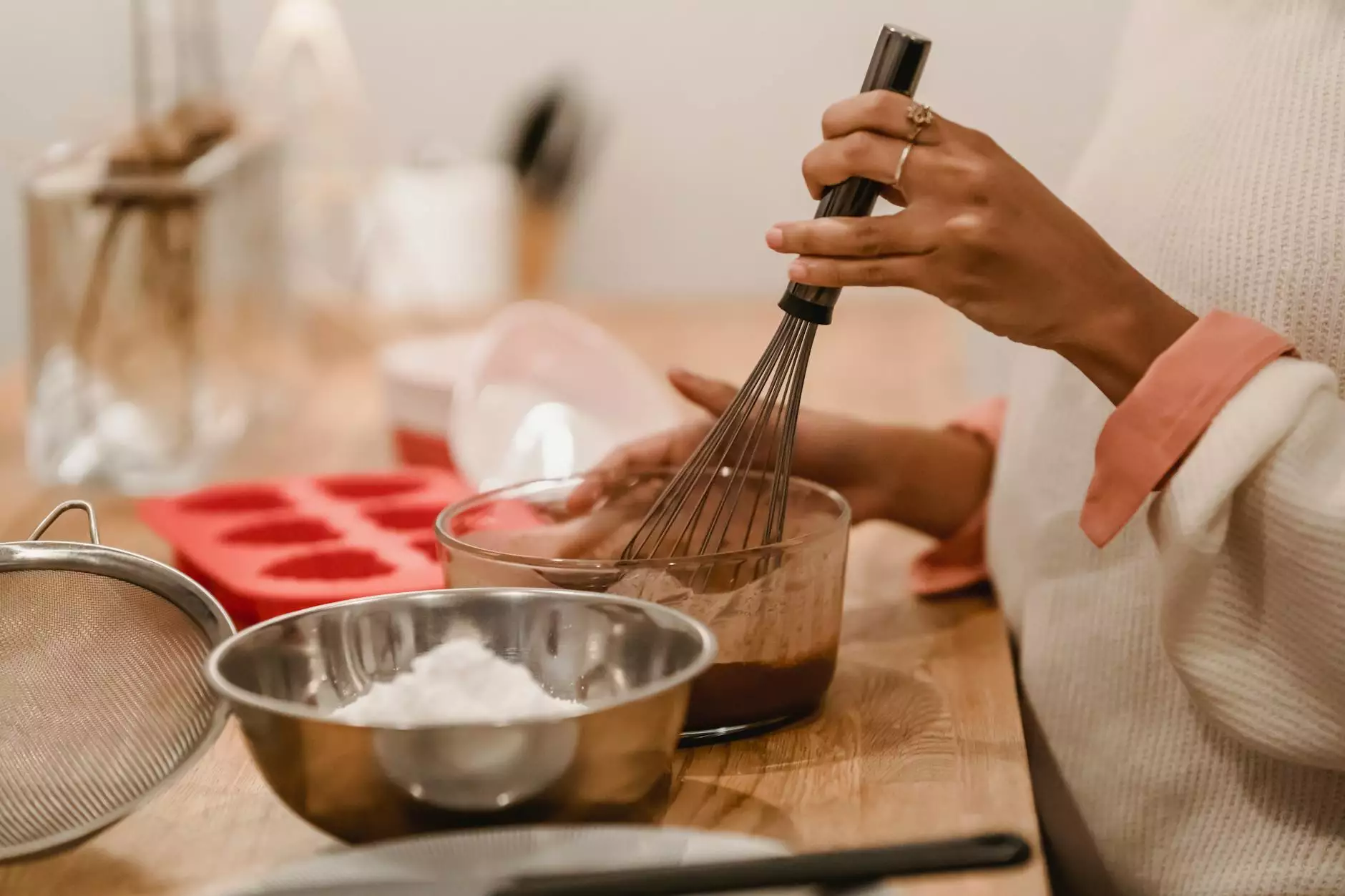
In today's fast-paced and competitive manufacturing landscape, the need for high-quality, efficient production methods has never been greater. One of the most innovative technologies available is the silicone injection machine, which plays a crucial role in various industries, particularly in electronics and medical supplies. This article aims to explore the importance, functionalities, and applications of silicone injection machines, as well as their benefits to businesses like Nolato.
What is a Silicone Injection Machine?
A silicone injection machine is a specialized piece of equipment designed to inject silicone materials into molds to create precise and intricately designed products. This process is essential for producing items that require durability, flexibility, and biocompatibility. Silicone injection molding technology is widely utilized in industries where quality and consistency are paramount.
Key Components of Silicone Injection Machines
To understand how a silicone injection machine operates, it's important to recognize its key components:
- Injection Unit: This component enables the precise injection of silicone into the mold. It includes a hopper that feeds silicone into the machine and a screw or plunger that forces the material into the mold cavity.
- Mold System: The mold system consists of two halves (the cavity and the core) that shape the silicone material. High-quality molds are crucial for achieving accurate dimensions and finishes.
- Clamping Unit: This unit holds the mold halves tightly together during the injection process to prevent leaks and ensure a smooth operation.
- Temperature Control System: Proper temperature control is vital in silicone injection molding to maintain the optimal viscosity of the material and prevent degradation.
- Control Panel: This interface allows operators to set parameters such as injection speed, pressure, and cycle times for efficient machine operation.
Applications of Silicone Injection Machines
1. Electronics
The electronics industry benefits tremendously from silicone injection machines, which are used to produce components like:
- Keypads: Silicone keypads made through injection molding are known for their durability and tactile feedback.
- Connectors: Silicone seals and connectors provide moisture and dust resistance, essential for the longevity of electronic devices.
- Encapsulation: Many electronic components are encapsulated in silicone to protect them from environmental factors and physical damage.
2. Medical Supplies
In the medical field, the precision and reliability of products manufactured using silicone injection machines are critical. Applications include:
- Medical Devices: Silicone is widely used to manufacture parts for medical devices, ensuring they are biocompatible and safe for patient use.
- Prosthetics: Custom silicone prosthetics can be produced to match the body’s anatomy, offering comfort and functionality.
- Seals and Gaskets: Silicone materials are utilized for seals and gaskets in medical equipment, providing airtight and watertight seals.
Benefits of Using Silicone Injection Machines
1. Precision and Consistency
One of the primary advantages of using silicone injection machines is their ability to produce highly precise and consistent products. This is essential in industries like electronics and medical supplies, where even minor variances can lead to functionality issues.
2. Scalability
Silicone injection molding is an ideal solution for large-scale production. Once the mold design is finalized, manufacturers can produce thousands of identical parts in a short time, significantly increasing productivity.
3. Material Versatility
Silicone injection machines can work with a variety of silicone materials, including different hardness levels and colors. This versatility allows manufacturers to customize products to meet specific client needs, enhancing their competitive advantage.
4. Durability and Performance
Products created using silicone injection molding typically exhibit superior durability and performance. Silicone resists various environmental conditions, including extreme temperatures, UV light, and chemical exposure, making it an ideal material for many applications.
The Process of Silicone Injection Molding
The silicone injection molding process can be broken down into several key steps:
1. Material Preparation
The silicone material is prepared and heated to the appropriate viscosity suitable for injection. This is a critical step ensuring that the material flows easily into the mold.
2. Injection
The prepared silicone is injected into the mold under high pressure, filling the cavities and taking the shape of the mold design. This step requires precise control over injection speed and pressure to avoid defects.
3. Curing
Once the mold is filled, the silicone needs to be cured. This can involve heating the mold to a specific temperature to ensure complete polymerization of the silicone material, resulting in a finished part that maintains the desired properties.
4. Cooling and Ejection
After curing, the mold is cooled before ejection. This process ensures that the finished product retains its shape and has balanced thermal properties.
5. Finishing Touches
Finally, any finishing processes such as trimming, surface treatment, or additional coatings may be applied to enhance the product’s performance and appearance.
Choosing the Right Silicone Injection Machine
When investing in a silicone injection machine, businesses must consider several factors to choose the right model:
- Production Volume: Assess the expected production volume to determine the size and capacity of the machine required.
- Mold Complexity: Different machines handle varying levels of mold complexity; select one that meets your product design needs.
- Material Compatibility: Ensure that the machine can accommodate the specific types of silicone materials you intend to use.
- Maintenance and Support: Choose a manufacturer that offers strong after-sale support and easy maintenance options to maximize machine uptime.
Future Trends in Silicone Injection Molding
The future of silicone injection machines looks promising, with several trends shaping the industry:
1. Smart Manufacturing
Integration of IoT and AI technologies will enable smarter manufacturing processes, allowing for real-time monitoring and optimization of production parameters.
2. Sustainability
With increasing focus on sustainability, manufacturers are exploring eco-friendly silicone materials and recycling processes, making the industry more environmentally friendly.
3. Innovation in Materials
Advancements in silicone formulations are leading to the development of even more specialized materials, catering to specific industry needs, particularly in biocompatibility and thermal stability.
Conclusion
In conclusion, silicone injection machines are a vital piece of equipment in the manufacturing of high-quality products across various industries, especially in electronics and medical supplies. Their precision, efficiency, and adaptability not only enhance production capabilities but also ensure that businesses can meet the ever-increasing demands of the market. As technology evolves, the role of silicone injection machines will only continue to expand, offering exciting opportunities for growth and innovation in manufacturing.
With companies like Nolato leading the way, investing in high-quality silicone injection technology will be essential for businesses wanting to maintain a competitive edge. Whether it's through enhancing product performance, increasing production scalability, or ensuring product safety in medical applications, the investment in silicone injection machines is a leap towards a more efficient and productive future.