Comprehensive Insights into Injection Mould Tooling in China
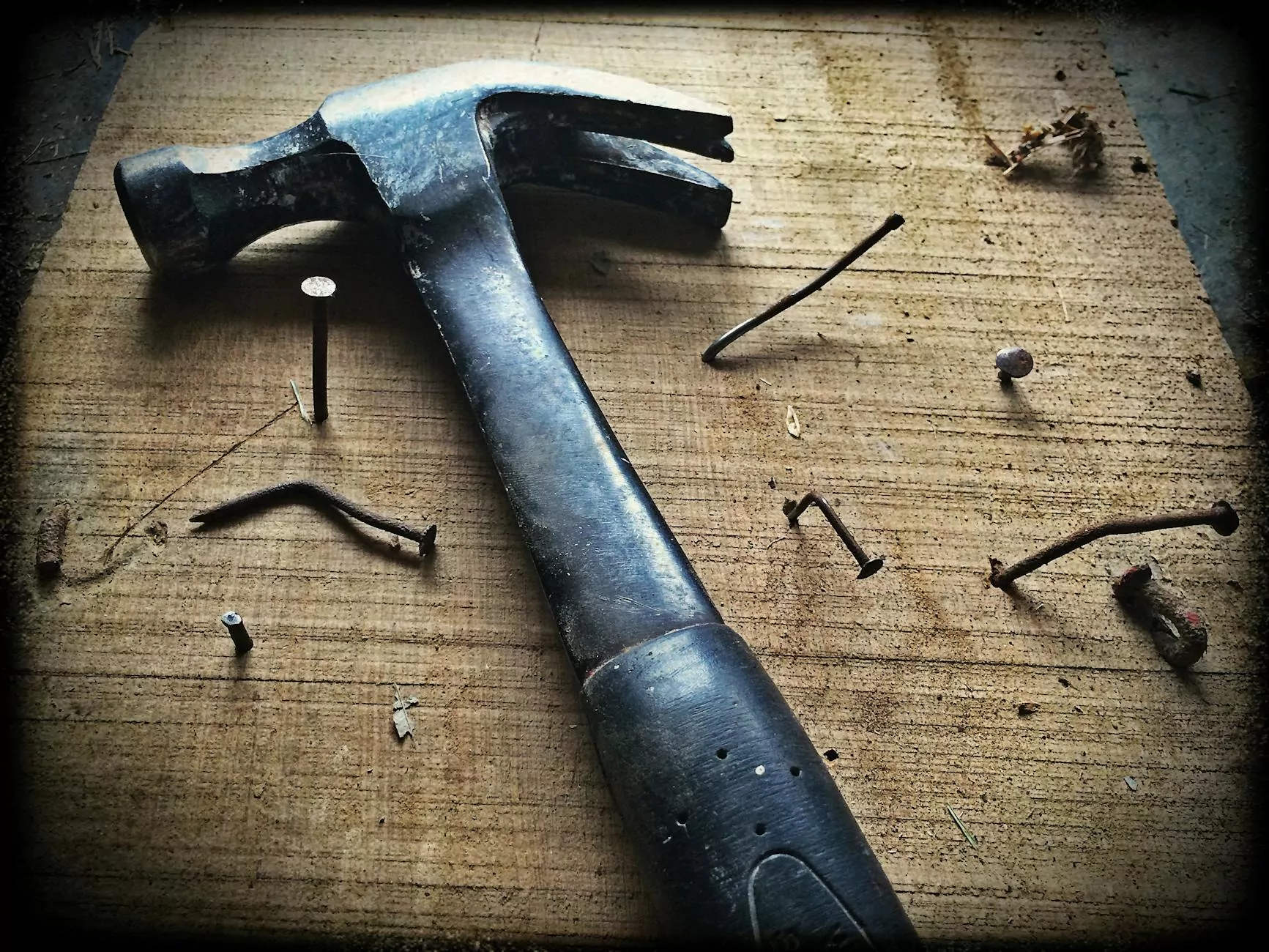
In today's globalized economy, injection mould tooling in China has become a cornerstone in the manufacturing sector. Manufacturing leaders around the world are now turning their attention to China, not just for its cost advantages but also for its advanced technological capabilities and skilled workforce. In this article, we will explore what injection mould tooling is, the intricacies of the process, and why China has emerged as a dominant player in this field.
What is Injection Mould Tooling?
Injection mould tooling is a process used to create parts by injecting molten material, such as plastics or metals, into a mould. This method is extremely important in the manufacturing of various products including automotive parts, consumer goods, and industrial components. It relies on specialized machinery and skilled technicians to ensure that the tooling process is meticulously executed.
The Importance of Injection Mould Tooling in Manufacturing
Injection mould tooling is critical in many industries for several reasons:
- Efficiency: This process allows for high-volume production, which can significantly reduce costs per unit.
- Precision: The tooling provides exact specifications for pieces, ensuring high levels of accuracy and quality.
- Versatility: With the capability of using various materials, injection mould tooling can cater to a wide range of applications.
Metal Fabricators and Injection Moulding
Metal fabrication plays a vital role in the injection moulding process. Metal fabricators are responsible for creating the moulds that will eventually form the products manufactured through injection moulding. The combination of raw metal materials and advanced processing methods enables the production of high-quality injection moulds that can withstand the repeated stress of production cycles. This collaboration between metal fabricators and injection moulding companies is essential for a seamless manufacturing process.
Why Choose China for Injection Mould Tooling?
Several factors contribute to China being a preferred destination for injection mould tooling:
- Cost-Effectiveness: Labor and manufacturing costs in China are generally lower than in many Western countries, providing an economic advantage for companies.
- Advanced Technology: China has invested heavily in state-of-the-art machinery and technology, enhancing the capabilities of its manufacturing processes.
- Skilled Workforce: The country boasts a large pool of skilled professionals who specialize in engineering, design, and production processes.
- Infrastructure: Robust infrastructure supports large-scale manufacturing, from logistics to supply chain management.
Steps Involved in Injection Mould Tooling
1. Concept and Design
The process begins with a concept where designers and engineers create detailed designs of the product using CAD (Computer-Aided Design) software. At this stage, considerations are made regarding the material, functionality, and aesthetics of the part.
2. Tooling Design
Once the product design is finalized, the next step is to design the mould. This stage involves determining the mould cavities, cooling channels, and any features necessary for creating the expected geometry of the final product.
3. Mould Fabrication
With the mould design in hand, metal fabricators begin to create the mould using high-precision machinery like CNC milling machines and EDM (Electrical Discharge Machining). This step ensures the highest level of accuracy and quality in the mould itself.
4. Testing and Validation
Before mass production, a test run is conducted using the ready mould to ensure that it produces parts according to specifications. Adjustments may be needed to address any issues that arise during this stage.
5. Production
After successful validation, the tooling is ready for full-scale production. This phase involves injecting molten material into the mould to create thousands of identical parts, showcasing the efficiency of injection mould tooling.
Benefits of Injection Mould Tooling in China
Investing in injection mould tooling in China offers numerous advantages:
- Reduced Time to Market: Quick turnaround times for prototyping and production can significantly reduce time-to-market for new products.
- High Production Rates: Capable of producing millions of parts in a single production run, injection moulding is unparalleled in terms of efficiency.
- Quality Assurance: Rigorous quality control processes ensure that the end products meet international standards.
Challenges in Injection Mould Tooling in China
While there are undeniable benefits, there are also challenges associated with injection mould tooling in China:
- Intellectual Property Risks: Companies must take precautions to protect their designs and trade secrets.
- Communication Barriers: Language and cultural differences could lead to misunderstandings during the project.
- Quality Control Variability: Ensuring consistent quality can sometimes be a challenge due to differing manufacturer standards.
How to Choose the Right Injection Mould Tooling Partner in China
Selecting the right partner is critical for success. Here are some tips:
- Research Qualifications: Verify the manufacturer’s credentials, experience, and technical capabilities.
- Request Samples: Ask potential partners for samples of previous work to assess quality.
- Assess Communication: Ensure they have clear communication practices that will keep you informed throughout the process.
- Check Reviews: Look for reviews and feedback from other clients to gauge their reputation in the industry.
Future Trends in Injection Mould Tooling
The future of injection mould tooling in China looks promising, with several trends shaping the industry:
- Automation and Robotics: Increased automation is set to improve production speeds and reduce human error.
- Eco-Friendly Materials: The push towards sustainability is driving the use of bio-based and recycled materials in tooling.
- Smart Manufacturing: Integration of IoT (Internet of Things) in manufacturing processes for real-time analytics and improvement.
Conclusion
In summary, injection mould tooling in China is not only important for producing high-quality parts but also represents a significant competitive advantage for businesses engaged in manufacturing. With the boundless opportunities provided by the skilled workforce, advanced technology, and cost-effectiveness, leveraging China’s strengths in tooling can drive business success and innovation. As the landscape continues to evolve with new technologies and practices, companies that adapt and invest wisely will undoubtedly lead the market.
For more information and to explore Metal Fabricators who can assist you with injection mould tooling, visit deepmould.net.
injection mould tooling china