The Revolution of Injected Molded Plastic in Modern Manufacturing
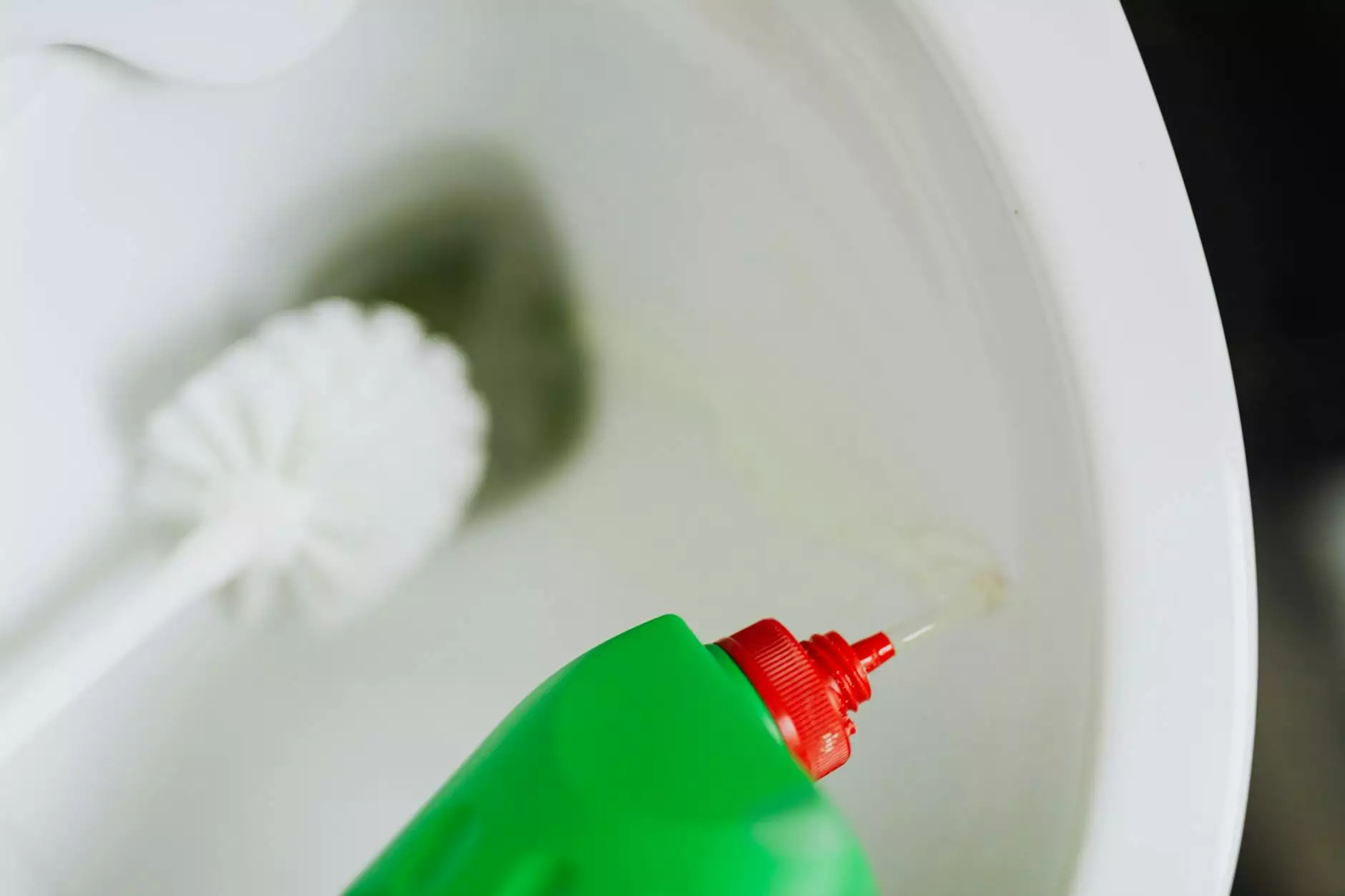
In the rapidly evolving world of manufacturing, injected molded plastic stands at the forefront, offering innovative solutions to traditional fabrication techniques. With the increasing demand for efficiency, durability, and design flexibility, businesses that utilize injected molding are seeing significant advantages over conventional methods.
What is Injected Molded Plastic?
Injected molded plastic refers to a manufacturing process whereby plastic material, typically in pellet form, is heated until it melts and then injected under high pressure into a mold. Once cooled, the molded part takes on the shape of the mold, allowing for the production of high-precision components with excellent surface finish and intricate designs.
The Injection Molding Process
- Material Selection: Various types of plastics can be used, including thermoplastics and thermosetting plastics.
- Melt Processing: The plastic pellets are heated in a barrel until they are molten.
- Injection: The molten plastic is forced into a mold cavity at high pressure.
- Cooling: The plastic solidifies as it cools within the mold.
- Ejection: Once solidified, the part is ejected from the mold.
Advantages of Injected Molded Plastic
The benefits of injected molded plastic cannot be overstated, especially for businesses engaged in metal fabrication. Some of the critical advantages include:
- Cost Efficiency: High-volume production reduces the per-unit cost significantly, making it an economical choice for mass production.
- Precision and Consistency: The injection molding process allows for tight tolerances, resulting in parts that are uniform and precise.
- Design Flexibility: Complex geometries and detailed designs can be achieved with ease, expanding the possibilities for product design.
- Material Variety: A wide range of plastic materials can be utilized, providing opportunities for innovative applications.
- Reduced Waste: The process uses only the necessary amount of material, minimizing waste compared to other manufacturing techniques.
Applications of Injected Molded Plastic in Metal Fabricators
Companies that operate in the field of metal fabrication, like Deep Mould, are beginning to recognize the potential of combining metal work with injected molded plastic to enhance product offerings. The following are some applications within the metal fabrication industry:
1. Automotive Components
The automotive industry demands high-performance, lightweight components. Injected molded plastics are used in the production of dashboards, bumpers, and other vehicle parts, thereby improving fuel efficiency and reducing overall vehicle weight.
2. Electrical Enclosures
In the realm of electrical engineering, the use of injected molded plastics allows for the creation of durable, insulated, and waterproof enclosures, protecting components from environmental factors.
3. Household Appliances
Many household appliances incorporate injected molded plastic components, from knobs and handles to internal mechanisms, providing durability and aesthetic appeal.
4. Consumer Products
Products that require intricate designs and custom colors, such as toys and gear, benefit immensely from injected molded plastics, giving manufacturers a competitive edge in design and functionality.
Why Metal Fabricators Should Embrace Injected Molded Plastics
The integration of injected molded plastic into metal fabrication processes forge new avenues for innovation. Here are several reasons why metal fabricators should consider embracing this technology:
1. Enhanced Product Offerings
By incorporating plastics into metal works, fabricators can diversify their product lines, offering more comprehensive solutions that appeal to various markets.
2. Improved Collaboration
Working with injected molded plastic enables fabricators to collaborate with a broader range of suppliers and industries, fostering innovation and ensuring that they stay competitive.
3. Future-Proofing
The ongoing demand for lightweight, efficient, and environmentally friendly materials will push more companies to adapt to these technologies, ensuring they remain relevant in the market.
Choosing the Right Partner: Deep Mould’s Commitment to Excellence
When selecting the right business partner for injected molded plastic solutions, Deep Mould stands out as a leader in the field. With a strong commitment to quality, innovation, and customer satisfaction, they exemplify what modern metal fabricators should aspire to:
- Expertise: Deep Mould’s team of experts boasts years of experience in both metal fabrication and molded plastics.
- State-of-the-Art Technology: Utilizing cutting-edge equipment, they ensure precise and efficient production techniques.
- Sustainability: Deep Mould is dedicated to eco-friendly practices, implementing sustainable materials and minimizing waste.
- Customized Solutions: Every project is tailored to meet specific customer needs, ensuring optimal results.
Challenges of Injected Molded Plastics
While the benefits are significant, it is also essential for businesses to recognize the challenges associated with injected molded plastic:
1. Upfront Costs
The initial investment in molding equipment and tools can be high, which may deter some businesses from entering this domain.
2. Material Limitations
Not all plastics are suitable for every application. Understanding the properties of different materials is crucial for success.
3. Process Complexity
The intricacies of the injection molding process require skilled professionals and precise monitoring to avoid defects.
The Future of Injected Molded Plastic in Manufacturing
As technology continues to mesh with manufacturing processes, the future of injected molded plastic is robust. With advances in materials science, such as the development of bio-based plastics and composites, we can expect to see even broader applications and greater efficiency.
Conclusion
In conclusion, the integration of injected molded plastic into metal fabrication presents a transformative opportunity for businesses looking to innovate and grow. With its many advantages, such as cost efficiency, precision, and design flexibility, the advantages clear. As industries continue to evolve, companies like Deep Mould will lead the charge, setting the standard for excellence in manufacturing processes.